电子束
用电子束加工金属有着悠久的历史:1879 年,William Crookes 爵士首次证明这项技术可以熔化金属。
电子束的深层焊接效应于1957年被发现。
不断的创新使电子束技术成为一种现代化的生产方法。可以涵盖广泛的任务——在不同的市场和行业中更精确、更高效、更经济。
实时 CNC 控制的稳定电子束可在无需额外材料的情况下以最小的能量输入和变形来焊接金属。这会在机加工零件中形成具有狭窄热影响区的深焊缝。与激光器相比,它提供了具有快速光束偏转的节能光束源。无论波长如何,粒子束都会耦合到各种金属甚至铜或铝的光学反射表面。
特点和优点:
对电子束的非常精确的控制
可以减少生产过程步骤
具有最高重复精度的恒定质量保证
先进的构造和设计选项
通过真空处理显着改善冶金性能
可用功率范围宽
电子束技术
多种光束特性和几乎无惯性的光束偏转:
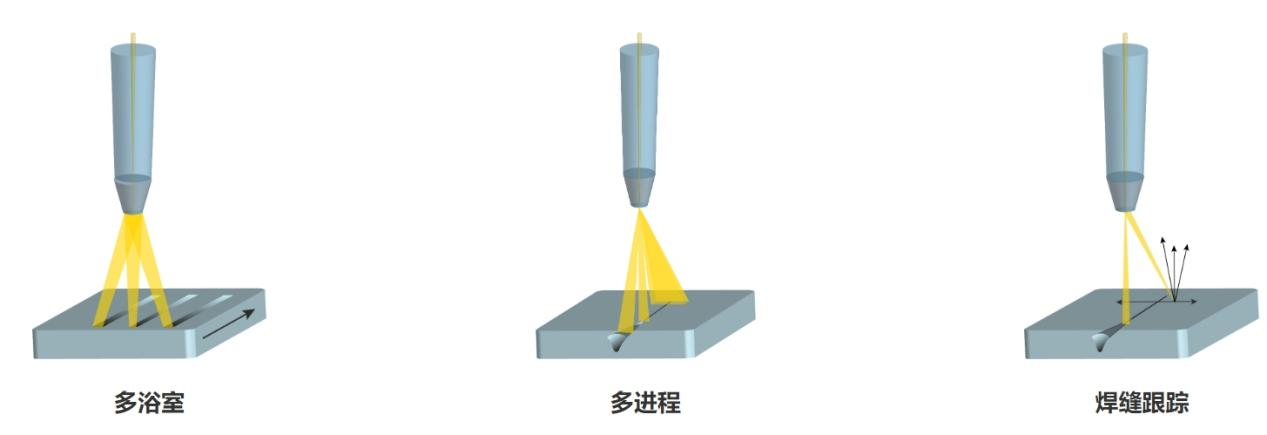
附加功能和优点:
焦点处功率密度极高,高达 10 7 W/cm 2
在生产运行中应用电子束的多种方式:
多浴、多工艺、焊缝跟踪、表面处理和成像
一机多用:焊接、钻孔、涂层和表面处理
机器和系统的多功能组合:
通用型、分度型、生产单元和连续带式焊接机
高能效:
与激光束焊接和其他焊接工艺相比,电子束加工可将更多的输入功率转换为光束功率。
计选项:
除了钢合金之外,它还可以用于防火合金和异物,以及减少工件的体积和质量。
真空条件显着改善冶金性能:
不需要任何辅助剂(例如保护气体等)来保护熔池或焊池不被氧化。此外,真空对焊缝的冶金性能有非常积极的影响,可以避免气孔的形成。
提供广泛的性能范围:
最佳适应应用的要求。
电子束加工的挑战:
为了最佳地利用电子束加工的可能性,提前处理该技术可能存在的缺点是有利的。
真空条件:
为了确保最短的抽空时间,泵的尺寸以及工件和真空室的清洁度至关重要。评估总体生产力时必须考虑疏散时间。
磁性:
电子束很容易被工件材料或装置的剩磁所偏转。这种影响可以通过调节电子束得到一定程度的补偿。此外,在将工件引入真空室之前,可以对工件进行自动消磁。
1、电子束焊接
电子束焊接(EB 焊接)可以产生非常深、细长且平行的焊缝。可以实现高焊接速度,从而最大限度地减少工件的热量输入。减少甚至避免了翘曲和曲率。
焊接是一种制造过程,其中材料(通常是金属或热塑性塑料)通过高温或高压或两者结合在一起,通过让零件冷却,从而使它们熔化。
并非所有金属都可焊接,而且,组合不同的金属会对可焊性构成挑战。
除了电子束焊接的一般优点(见下文)外,该技术还显着扩大了看似“不可焊接”金属的范围,例如难熔金属、化学活性金属和反射金属。
电子束焊机中常见的真空条件对焊缝的冶金性能具有非常积极的影响。
两种材料的电子束焊接:
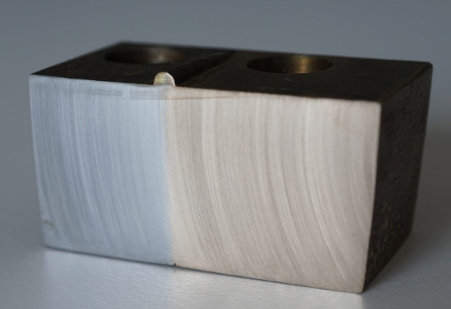
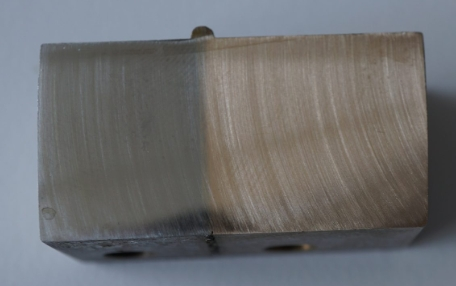
电子束焊接原理:
在焦点处,电子束将工件材料加热到其熔点以上并使材料蒸发。电子的动能转化为热量。
焦点尺寸可达 100 µm。在那里形成蒸汽毛细管,其周围有熔化夹套或焊池。
随着电子粒子束前进,蒸气毛细管进一步移动。在移动毛细管的前部,材料不断熔化并移动到后部。熔化的材料在那里凝固。
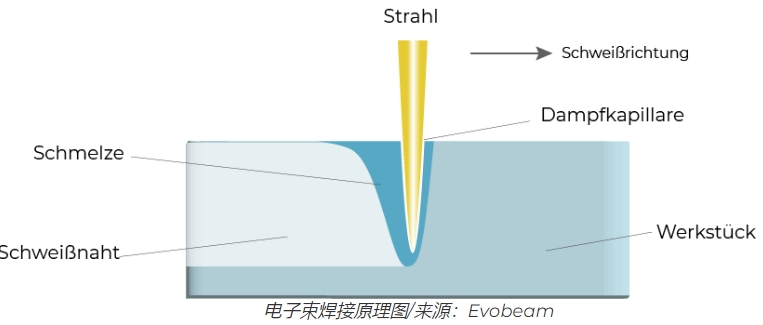
电子束焊接性能及优点
电子束焊接提高了焊缝的精度和耐用性:
焊接工艺室中 大约 10 -4 mbar的高真空条件:
真空对熔融材料进行脱气,从而最大限度地减少熔化区域中的孔隙或污染。不需要气体或焊剂来保护焊池免于氧化。
非常通用的电子束特性:
可以精确控制聚焦平面、电子束功率强度和几乎无惯性的电子束偏转等参数。这提高了焊接工艺的接缝质量和生产率。
高达 200 毫米/秒的高焊接速度最大限度地减少了工件的变形:
电子束在几毫秒内以极其局部集中的方式加热工件,从而形成狭窄的焊缝和热影响区 (HAZ)。
多种可焊接金属:
除了钢和钢合金外,电子束还可以焊接化学活性金属(例如钛、锆、铍),甚至难熔金属(例如钨、钼、铌)。由于无论波长如何,电子粒子束也会耦合到光学反射表面,因此它也可以毫无问题地焊接铜。
节能焊接工艺:
电子束机将大约 60% 至 70% 的连接功率转换为焦点处的电子束功率。与其他焊接技术相比,例如 例如,激光焊接或电弧焊接、电子束焊接更加节能。
焊缝深度与宽度之比高达 16 的深焊:
高达 10 7 W/cm 2的高功率密度 在蒸气毛细管底部产生高达约 3,500 °C 的温度,从而实现深焊电子束的影响。可焊接长达 250 毫米的钢和长达 500 毫米的铝。
全自动焊接:
全自动电子束焊接系统可实现每个工件相关参数的精确重复性和完整可追溯性。这意味着每个单独零件的焊接过程都可以得到安全控制和记录。这对于航空航天业等经过验证的流程至关重要。这不仅适用于飞机和航天器原始设备的生产,也适用于MRO(维护、修理、大修)。在这里,电子束焊接通过最大限度地减少热量输入和部件变形,同时保持高焊缝强度,使维修变得更加容易。
真空室(工作室)有不同尺寸可供选择:
EVOBEAM 电子束焊接系统的真空室精确适应应用。这可以最大限度地减少体积、抽真空时间、加快焊接周期并提高生产率。
电子束焊接附加信息
激光束焊接还可以覆盖电子束焊接的一些应用领域。
然而,激光束的能量效率比电子束低,并且提供的光束功率较低。
此外,激光束将功率耦合到有色金属(例如铜)的效果非常差。
对于焊接深度较小的大型钣金零件,激光束也可以在大气条件下工作。
各种研究和工业应用表明,真空中的激光焊接可以更好地将激光束能量耦合到钢材中,从而优化焊缝深度和质量。
Evobeam 还提供真空激光焊接机器和系统。
我们可以为相应的真空焊接应用提供最佳解决方案,以实现高生产率:经济高效、快速、多功能且具有最高的焊接质量。这就是为什么近年来我们成功地向要求苛刻的航空航天和汽车行业等提供我们的解决方案。
2、电子束钻孔
电子束钻孔(EB 钻孔)提供了令人印象深刻的灵活性和质量组合。射流以最高速度移动并形成非常干净的通孔。此外,每个孔可以具有不同的尺寸。这些功能可实现生产力最大化。
电子束钻孔是一种热处理工艺,可形成 100μm 至 2mm 的小通孔。由于 EB 的高能量特性,可以实现高达 25:1 的极高 T/D 比(深度与直径)。
高 T/D 比和快速钻孔速度的结合使 EB 钻孔有别于所有其他用于生产小孔的机械、化学和其他热技术。
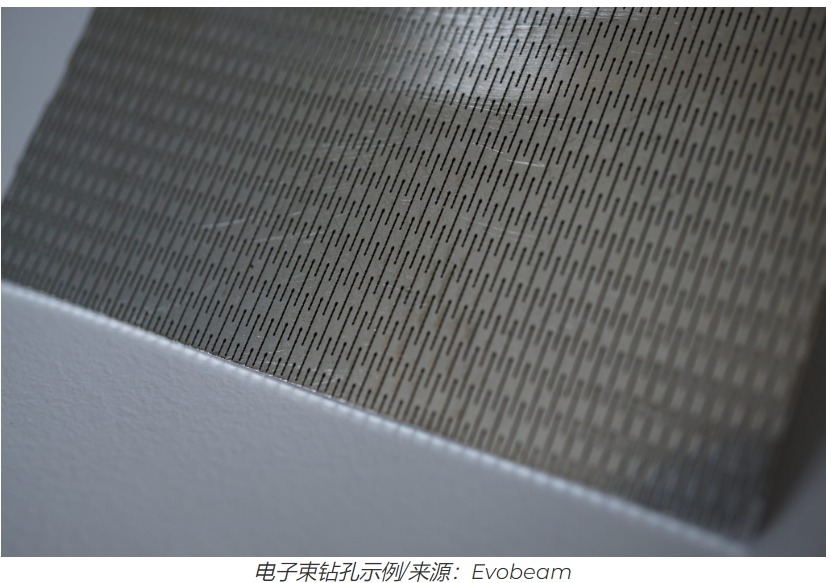
电子束钻孔原理
来自电子束的能量输入导致蒸汽毛细管的形成。该毛细管可以穿透整个工件。
电子束关闭后,蒸汽射流消失,熔体再次关闭毛细管。为了形成通孔,必须快速吹出熔化的材料。
这是通过在工件背面施加一层爆炸性汽化材料来实现的。由于这一重要方面,EB 钻孔无法产生盲孔。
所描述的原理还解释了所得的孔并不完全是圆柱形的。在许多产品和部件中,不需要圆柱孔,也不需要盲孔。这尤其适用于过滤应用:例如纸浆和造纸、食品和饮料加工、废水等。事实上,EB 钻孔的其他特性远远超过了所提到的缺点。
电子束钻孔特性及优点
电子束钻孔具有多种特性,这些特性对钻孔特性以及灵活性和生产率方面的结果产生有益影响。
高速钻孔:
根据工件的特性以及钻孔深度和直径方面的参数,电子束钻孔可以非常快速地进行:例如每秒 5,000 个孔,钻孔深度为 0.1 毫米或钻孔深度为 8毫米仍然约为每秒 5 个孔或每分钟 300 个孔。
极其通用的电子束特性
由于电子束的特性,转换到工件中的能量几乎与表面上的电子束方向无关。此功能允许您钻斜孔或有角度的孔。此外,如果需要,每个孔的直径可以不同,这意味着 EB 的多功能性允许在不更换钻孔工具的情况下钻出不同直径的灵活孔图案。
可钻孔的材料范围非常广泛:
除了钢和钢合金外,还可以对化学活性金属(例如钛、锆、铍)甚至难熔金属(例如钨、钼、铌)进行钻孔。由于无论波长如何,电子粒子束也会耦合到光学反射表面,因此也可以使用电子束轻松地对铜进行钻孔。
高 T/D 比(深度与直径)高达 25:1
电子束可实现非常窄和深的通孔的热钻孔工艺。
电子束钻孔附加信息
通过 EB 钻孔形成的通孔的具体形状特征是整个孔深度上有轻微的锥度。除其他特性外,这使得电子束钻孔特别适合过滤应用.
3、电子束沉积焊
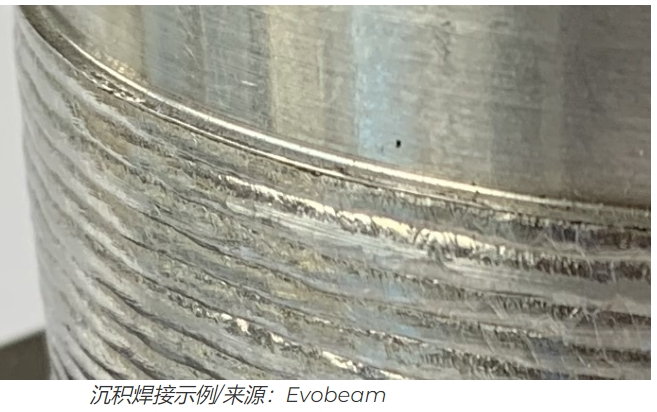
电子束沉积焊接(EB沉积焊接)可以精确添加材料的剂量并调整层厚。这支持在成型和硬度方面精确控制材料特性。
使用电子束的沉积焊接是一种热工艺。
这会将粉末或金属丝等金属直接插入熔池中。真空条件细化所得表面结构,以提高基材的硬度和耐腐蚀性。
电子束沉积焊接原理:
电子束的动态偏转选项使得可以处理更大面积的工件。
在焦斑中,电子束熔化工件和填充材料。电子束的高频偏转熔化金属的限定区域。
为了优化新层的化学和冶金性能,精确控制和调整光束功率和光束直径参数至关重要。电子束技术是实现这一点的理想选择。
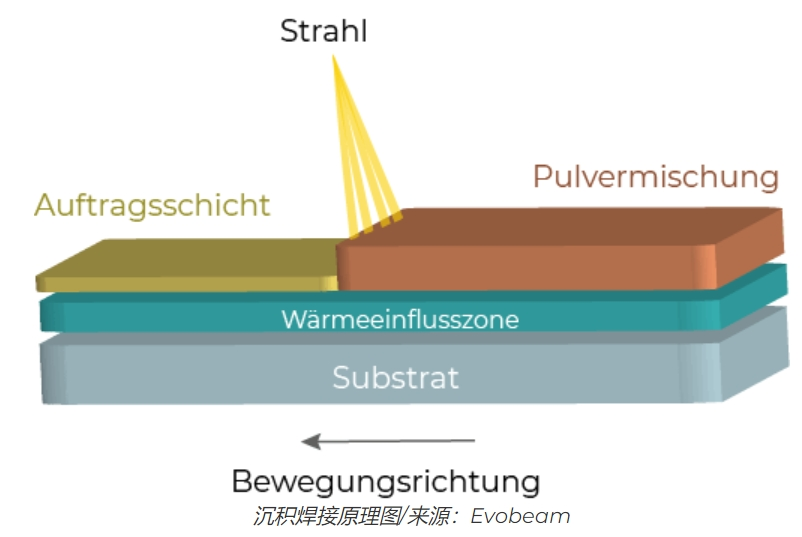
电子束沉积焊性能及优点:
电子束沉积焊接对所得材料性能和生产率具有积极影响。
控制层厚度:
精确的电子束特性控制能量密度和分布,从而控制粉末作为附加材料的电镀层厚度。
定义的材料属性:
可以通过精确的能量输入和层厚度来控制硬度和耐腐蚀性。
镀层表面和结构精细化:
电子束电镀时的真空条件对镀层表面和结构产生积极影响。
全自动电镀:
通过全自动电子束沉积焊接,每层参数都可以精确重复并完全跟踪,因此每个工件的整个过程都得到可靠的控制和记录
电子束沉积焊接附加信息
沉积焊接可以被视为一种增材制造方法。然而,重点是通过添加单层或多层材料来改变给定工件表面的材料属性。
4、电子束表面处理
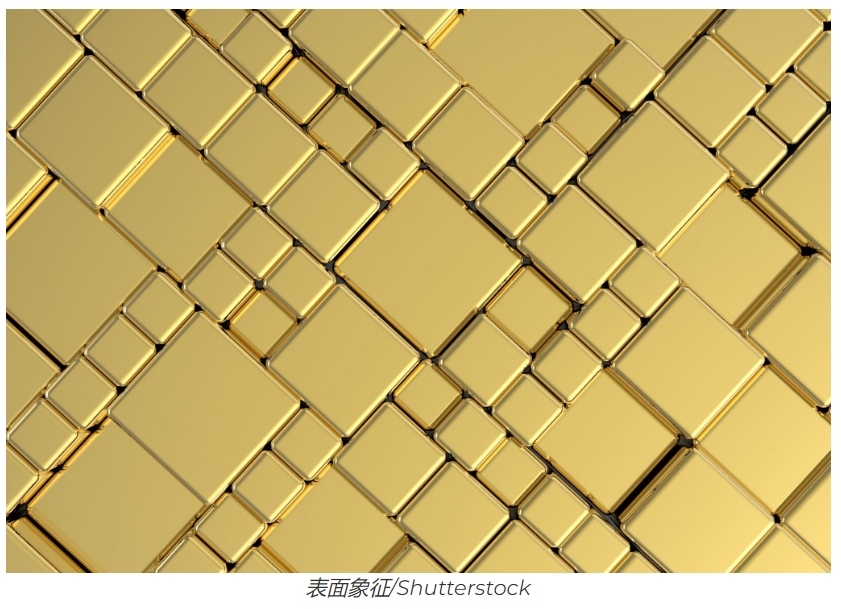
咨询电话:13522079385
电子束表面处理
电子束表面处理提供了多种方法:
硬化、重熔、表面结构化、雕刻和抛光。
它们都可以非常精确和有效地应用。此外,这些可以集成到一个系统中,从而实现系统的最大利用率。
工件表面是与其周围环境的物理界面或边界。这可以是环境(例如气体、紫外线、液体、湿气、辐射、腐蚀性溶剂等)或其他材料(例如金属、非金属等)。
表面处理的目的是提高工件小面积或大面积表面的耐腐蚀性、硬度和外观。
喷砂技术可精确且可重复地修改该表面。
电子束表面处理原理:
根据应用和所涉及的材料,会产生不同的效果。
硬化:
射流将界面加热到奥氏体温度以上。热量流入周围较冷的物体,使其迅速冷却。这种自淬火不需要额外的冷却剂。光束的高功率密度在局部产生必要的温度梯度。也可以保持在熔点以下并迫使结构发生变化,同时工件表面保持固态。
重熔:
射流将界面加热到熔化温度以上,并对合金进行改性或分散不溶性硬质颗粒,例如 WC。
表面结构化:
射流将材料熔化至规定深度并形成凹槽图案。这些具有规定表面粗糙度的可自由设计的图案非常重要,例如,对于医疗应用来说,可以最大限度地减少细菌膜。
雕刻:
精确控制的光束可以作为主要工艺步骤或在完成另一个光束加工工艺后对工件进行雕刻。雕刻可以精确定位并以可见且机器可读的方式标记工件(例如数据矩阵等)
抛光:
对导热性差的材料(例如钛)进行机械抛光可能会导致局部爆燃。喷射通过仅熔化和控制界面并提高平滑度、光泽度和硬度来实现积极的结果。
电子束表面处理的特性和优点:
电子束表面处理提供了以所需方式修改表面特性的绝佳机会。
工作过程室中 约 10 -4 mbar的高真空条件:
真空对熔融材料具有积极的影响,可导致脱气并显着减少熔化区中可能存在的孔隙或其他污染物。
极其通用且可控的光束特性:
通过精确控制聚焦程度、光束功率强度和几乎无惯性偏转等光束参数,可以精确调整电子束并在表面上精确移动。这是在结构和冶金性能方面表面特征发生可控且可重复变化的先决条件。
全自动表面处理:
电子束表面处理系统是全自动的。在每个工件表面本身的修改过程中,它们能够实现极其精确的重复性和相关表面处理参数的完全可追溯性。可以安全地控制和记录每个工件的表面处理过程。这对于航空航天业等经过验证的流程至关重要。这不仅适用于航空航天原始设备的生产,也适用于 MRO 操作(维护、修理、大修)。在这里,电子束技术通过极低的热量输入和部件的低变形促进了表面处理过程,同时提供了极好的可预测的表面特性。
真空室有不同尺寸可供选择:
EVOBEAM 电子束处理系统的真空室尺寸可适应各自的应用要求。这最大限度地减少了体积,从而减少了抽真空时间。这对于缩短整体焊接周期时间和提高整体生产率具有重大影响。
电子束表面处理附加信息:
近年来,利用电子束技术对表面进行受控和精确的改性似乎受到越来越多的关注。
除了上述应用之外,医疗行业或其他卫生标准极高的行业尤其受益于电子束技术的表面处理。这里的重点是避免细菌在表面定植。对于假体或植入物来说,优化的表面结构对于与骨组织的良好结合至关重要。
对于真空表面处理的特定应用,我们可以提供高生产率的最佳解决方案:经济高效、快速、多功能且具有最高的精度。