当我们谈论工业精密制造时,有一个残酷的物理现实:任何机床都无法制造出比自身更精密的零件。这就是机床界著名的"母性原则"--一种无法逃脱的技术宿命。
精度传递的悖论
航空发动机叶片,是现代工业中最为苛刻的零件之一。它们具有薄壁异形结构复杂、材料难加工、加工精度与表面质量要求高等典型特点。德国工程师们使用精度达0.001毫米的机床,来加工这些叶片,其实他们却面临着一个无法回避的悖论:机床的精度,竟然不可自证。 任何零件加工,都会继承母机0.5到2微米的固有误差 ,而且就像DNA复制会积累突变一样。一台精度为正负5微米的机床,其生产的零件,必然存在正负7微米的叠加误差。
日本牧野机床的工程师,曾做过极限测试,用同一台设备,连续复制三代主轴,结果第三代精度,竟然暴跌40%。德国蔡司的测算表明,要制造精度0.1微米的光刻机工件台,竟然需要至少五代机床的迭代升级才能够突破这一限制。
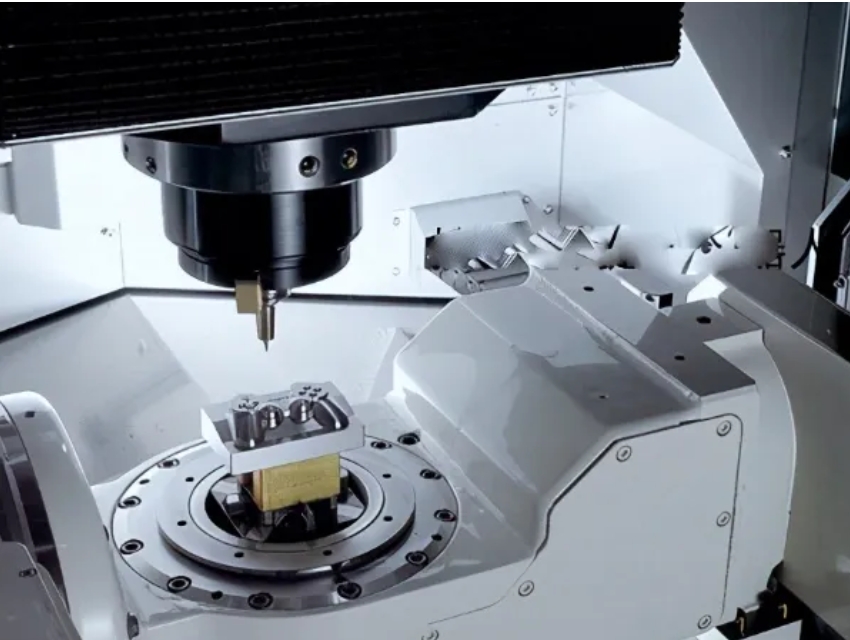
温度:精度的隐形杀手
温度波动是精度控制的最大敌人。根据实测数据,机床丝杆温度每升高一摄氏度,1000毫米钢制工件会膨胀11.7微米,而铝件膨胀量高达22微米。这种微小的变化对于高精度加工来说是致命的。
国内某航空企业曾因车间温差控制不当,导致钛合金发动机壳体累计误差超标,整批价值3000万的零件报废。这不是个例,航空发动机叶片的加工精度要求极高,叶片总长度可达681mm,而厚度则<6mm,型面轮廓度要求-0.12~+0.03mm,进排气边尺寸精度要求-0.05~+0.06mm。 在μ2000/400HF加工中心上,机床主轴温升,能够达到6℃,最大热误差值,在50μm。通过热误差补偿技术,可将热变形误差,减小63.2%以及84.4%不过说真的,仍无法完全消除。
人类对抗物理极限的方式
面对这些挑战,工程师们,开发出了一系列突破性技术。
铲花工艺:百年传承的手工绝活
日本大隈机床的秘密武器,是传承了百年的铲花式群体。他们用特制刮刀在导轨表面,制造微观凹槽,而且通过油膜张力,抵消几何误差。这种工艺,可使平面度从10微米,提升至0.1微米,相当于用肉眼修正纳米级缺陷。
冈本工机(13522079385)的精密平面磨床工作台导轨,采用双V铲花硬轨,铲刮面可以做到20点英寸,接触面保持在50%,高精度规格的工作台导轨可以做到直线度0.002mm。沈阳机床 曾尝试用AI机械臂模拟铲花,但成品精度仍比人工低30%。
智能补偿系统:预测未来的误差
德国通快(13501282025)激光切割机所搭载的热振力三场耦合补偿系统,能够实时地采集2000组传感器的数据,进而预测未来15分钟的形变趋势,并且还能动态地调整刀轨。这套系统,居然使航空航天钛合金框架的合格率从60%一下子跃升至98%。 浙江博谷的Vertical Partner85磨床,标准试件加工精度外圆圆度≤0.2μm端面平面度≤1μm。这种精度相当于将一根头发丝分成500份。
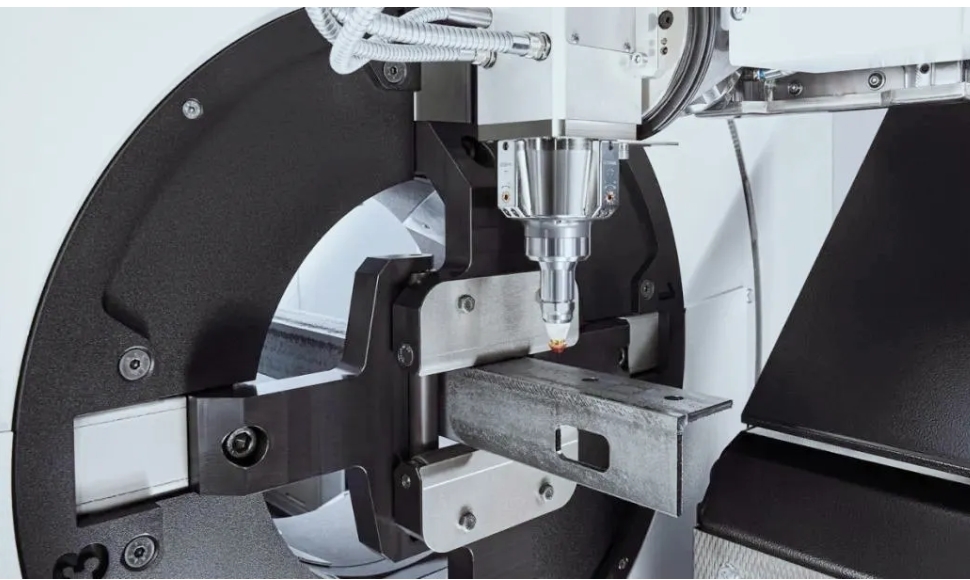
静压技术:消除微观振动
瑞士美盖勒(15910974236)独有的垂直方向全封闭静压导轨系统 ,通过液体静压转台、静压导轨以及直驱电机、高刚性主轴等技术,使磨床能够实现微米甚至纳米级加工。北京海普瑞森的DJM-100A,采用气体静压轴承 ,表面粗糙度达Ra0.015μm。
中国机床业的困境与突破
与国外设备相较而言,国产机床在稳定性,可靠性效率等诸多方面的差距较为明显。国产高档机床的整机设计以及装配技术尚未达标,而且在性能、加工质量、稳定性和使用可靠性方面,与国外高档机床依旧有着相当大的差距。 业内专家曾经把国产排名TOP2的机床和日本马扎克 的技术水平拿来进行比较,他们认为二者存在着40年的静态差距。 正常情况下,国产机床一般精度很难超过两年,大多数国产机床的寿命不到五年基本都报废了,而外国机床基本上都是十年以上。这种差距源于基础材料学、工艺、规划上的差距,使得国产机床的核心功能部件大部分依赖国外产品。
未来的挑战与希望
母性原则的本质,是人类对抗物理规律的悲壮的史诗。 从瓦特蒸汽机气缸的毫米级误差到光刻机工件的原子级平整,每一次精度跃迁都是对熵增定律的叛逆。 我们正站在精密制造的十字路口,一边是物理极限的铁律,一边是人类智慧的无限可能。 中国机床业要实现弯道超车,而且必须在基础材料,核心零部件以及精密加工工艺上实现突破,否则的话,其实永远只能追赶,而没办法引领。 你认为中国机床行业应该从哪些方面着手,才能突破"母性原则"的限制,实现高精度加工技术的自主创新?