随着动力总成各组成零部件结构的日益复杂化,以及量产总数的日趋减少,动力总成的生产无可避免地会遇到很多加工问题和技术难题.热套技术因其特殊的加工工艺,则可很好地应对和解决该领域内的诸多生产需求和难题.如通过热套技术将凸轮或齿轮安装到轴上可明显降低组件重量的同时,又可以确保轴类件拥有更高的精密度,而且可以生产那些需要高转矩和高动态载荷的工件.埃马克集团旗下的自动化公司的专家经过多年的努力,研发出热套专利技术,为汽车动力总成的生产提供了独有的柔性化加工解决方案.
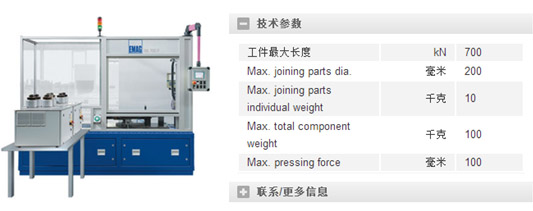
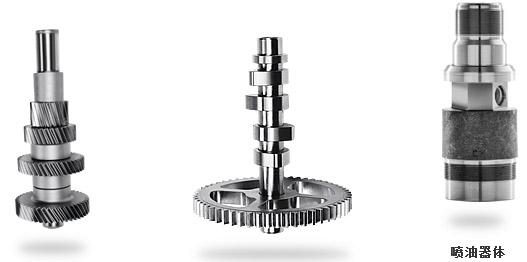
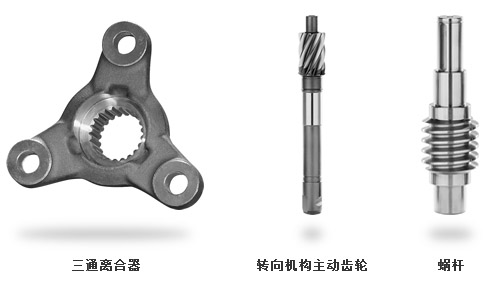
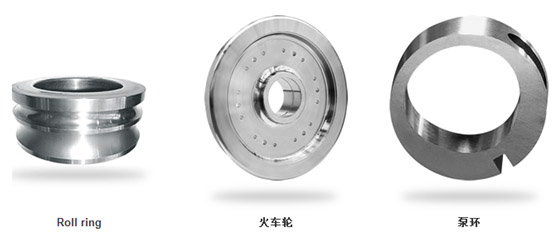
相较于单一材料凸轮轴,组合式凸轮轴因其较轻的重量,在市场上一直保持着良好的发展前景。如今,组合式凸轮轴已广泛运用于重型货车领域。然而,许多组合式凸轮轴的装配工艺通常需要较高的套装力,从而导致凸轮定位和校准中出现超标的误差。对此,埃马克能提供一种具有绝对优势的解决方案,即通过其专利技术――热套工艺,保证凸轮轴、齿轮轴和其他精密组合式部件能够完全精准地进行生产。这一生产技术的特点是无需进一步的加工。无论是要将控制凸轮或者齿轮装配到轴上或者要将轴装配到壳体中,预加热和装配技术都是安全持续的工艺。

埃马克技术的优势在于预加热组件,组件可以完全贴合工件并且温度可控。组合式凸轮轴的优势众所周知:价格更低、重量更轻、可选用不同材料生产、生产过程也更加灵活并能轻松使用新几何形状的凸轮,例如负半径等。出于减少汽油使用和降低二氧化碳排放的需求,组合式凸轮轴的使用在未来将会更加普遍。但是,套装凸轮和轴的替代工艺存在一个严重问题:两者无法高精度套装在一起,进而无法避免后续的精磨工序。在许多情况下,将凸轮套装到轴上都需要“适型”的工艺,如压装工艺过程中,滚花、花键或锯齿齿轮的要求。压装过程产生的压装力可能使工件变形,并导致凸轮定位和校准过程出现超标的误差。
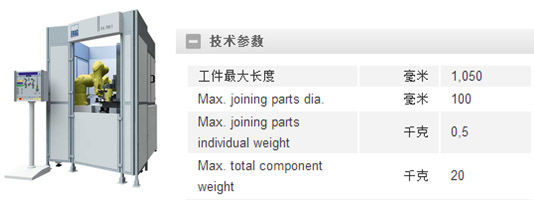
埃马克热套工艺装配代表精确套装热套,即通过热收缩将凸轮套装在轴上,可确保进行无阻力的套装,以达到规定的公差。此工艺的关键在于要严格控制“温度”和“时间”等工艺参数,以及套装设备的机械设计。当上一个凸轮被热套时,下一个已经在预热。配备一定预热装置的热套机床使得热套技术能够有效地应用在生产任务中。将机器人与特殊的夹紧技术的完美结合能实现误差小于15微米。
此原理能使凸轮轴设计者在设计时更加灵活,并且可确保能应用在工件类型频繁变化的中等批量生产中。高精度的组合式凸轮轴大大减少了继续磨削的必要性,如果使用精密的成品凸轮,甚至可以完全不需要精磨。
此工艺的另一优点在于可以使用不同材料生产组合式凸轮轴,包括使用100cr6材质的锻造凸轮、精磨成品凸轮,甚至是尺寸精确的粉末冶金凸轮,无需再进行精磨工序。此外,配套零件如堵头和端件也可以用性价比更高的材料制造。埃马克热套工艺能使凸轮轴适应发动机需求,并且优化负载能力和生产成本。
将机器人与特殊的夹紧技术完美结合能实现误差小于15微米工序延伸当凸轮轴在热套工序后需要磨削,热套机床可以连接到一台磨床,埃马克vtcds系列磨削中心让这一切变的非常容易:热套机床的机器人将加工好的凸轮轴直接传送到磨削中心的装载区上料位置。埃马克提供的这种工艺优势也能用于对其他零件的加工。
当加工齿轮轴时,被磨削后的齿轮能紧密地结合到轴上,不需担心砂轮造成误操作。同时,也能够最大程度地减少轴长,使得整个零件更加紧凑。
快速套装造就最佳品质埃马克的热套工艺能将灵活性和生产性完美结合,而设计的自由和对生产技术的选择能保证较短的节拍。当前一个凸轮被热套时,后一个凸轮已经在预热。配备一定数量预热装置的热套机床使得该技术能够有效地应用在生产任务中。正是埃马克热套机床所具有的以上优点使得许多凸轮轴生产商以及其他精密部件的生产商对热套新工艺表现出极大兴趣,有些企业正在进行加工测试,还有一些甚至已经将埃马克的全新工艺投入到生产。
在理想的情况下,客户将受用埃马克集团提供的效应,并且寻求从预加工到热套及最终加工的完整工艺。齿轮间的紧凑接触可保证齿轮轴的组件紧凑设计及高功能性密度热套技术的优点:高精度,热套后不需要后续工艺节省材料,减轻重量热套后不产生变形可组合不同材料的零件可自由选择工件套装顺序可自由选择角度和轴向位置可快速进行工件换型组合式凸轮轴的优点:价格更低重量更轻可使用不同材料制造凸轮更具生产灵活性更易生产新型几何形状的凸轮,例如负半径凸轮。